"You've Designed This Wrong!"
- Jon
- Oct 30, 2020
- 3 min read
Updated: Oct 31, 2020
Since starting this project last year it has been a truly exciting learning curve. It feels like 3D printing is starting to become more and more mainstream as people see the exciting possibilities on offer from the technology that is getting better and more affordable everyday.
One of the things I enjoy is the ability to try different approaches to solving the problems associated with model aircraft, namely; strength and weight.
I had an email this morning from someone telling me that I had done it 'wrong'. In this case we were talking about using infill to provide the support structure through the wing. 'Wrong' implies that as a design solution it fails to solve the primary problems, strength and weight. Given that these aeroplanes fly using this method clearly indicates that the problems of strength hand weight are satisfied. (In fairness he was refering to the Avanti, which I haven't flown but was complaining about the design methods themselves.)
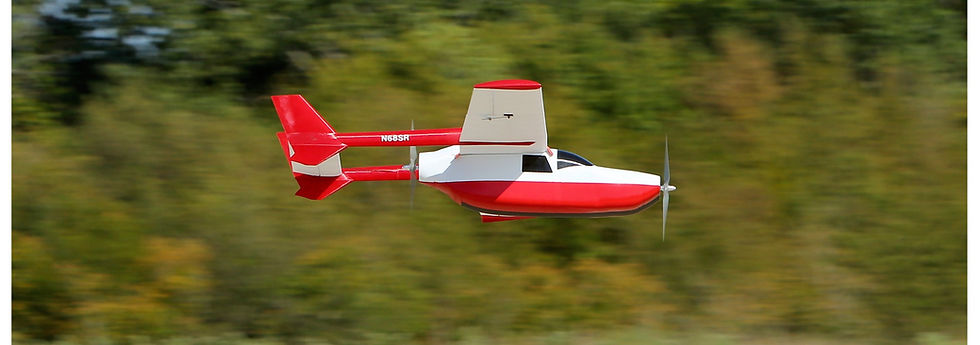
I think I understand where this comes from. For many years, if you were going to build model aircraft at home you would use balsa wood, arranging pieces such that you had traditional spars and ribs, this is the model aircraft design dogma. Where does it say that this is the only way to do it? New technologies should free us up to try different things. You would struggle to strengthen your balsa wing by setting wood into a 3 dimensional cubic arrangement.
I am not saying that my way is right, in fact I am trying to argue that there isn't a right way, each method of solving the primary problems of strength and weight has its pros and cons. I have used different solutions throughout my models and, some models I have in development use both defined wing structure with spars AND slicer infill.
I understand the cons associated with the infill method too.
INFILL METHOD
PROS:
- Quick(er) design process.
- Strong. The cubic pattern in particular provides strength in all directions.
- Flexibility of design. In other words you can increase or decrease as necessary. Also buy increasing the infill print speed you can lighten the infill. I usually use double the wall speed.
- Easier to print and with faster print times.
CONS
- Non-specific support. Sometimes support is needed in a particular place, this can be overcome by adding a wall (cut) in especially.
- Weight, not always, but can be heavier.
- Allows an element of variability in printed weight due to the variety or printers, settings, etc. I have printed the same part and found it 30% heavier after changing a single Cura setting.
- Any channels cut out for control runs, etc, actually add to the weight by introducing a new wall. this also increase print time.
The alternative I'll call the defined structure method.
DEFINED STRUCTURE
PROS:
- Targeted support. You can make sure there are supports exactly where they are needed
- Printed weight is more stable from machine to machine.
- In some circunstances it is lighter. I found a 7% saving on a wing part that had many channels required (this increases infill method weights). Simpler wing parts have proven to be heavier!
- Strong.
CONS
- Considerably more design time. Whilst this is not neccessarily of concern to the end user, design time should be considered. I can certainly make models available cheaper if they take less time to design.
- Potentially longer print times, and more complex prints with more retractions etc.
- Not always a weight saving depending on the part in question.
I think there is room for both techniques and also the hybrid technique whereby we define some structure where needed but use infill where we don't. Ultimately I believe the blending of these techniques will be best suited to solving the problems of strength and weight.
The email I received this morning was less than tactful in telling me what they thought, (perhaps he forget that another human who spent a fair amount of time on this work was going to read it?) but I am always willing to receive feedback on these designs. Tell me your ideas for how we design planes for 3D printing going forward.
Hallo, gibt es in naher Zukunft ein Update mit folgenden Punkten:
Öffnung im Rumpf zum Akkuwechsel ohne die Tragfläche ab zu bauen.
Befestigung der Tragfläche ohne Gummi.
Servohalter in der Tragfläche ähnlich wie in der Howard DGA-5.
Grüße aus Bayern
Heinz
Hi Jon,
I'm looking for help to develop an RC airplane, inspired by the Piaggio Avanti you mentioned earlier.
The concept is as follows: - An electric canard aircraft with 2 propellers close to the centre line (to minimize asymmetry if one engine stops). - The configuration is a low-wing with short landing gear (low C.G.), heavier wing loading (no flaps), and a wide stance for stable take offs and landings. - The propellers are totally protected by the main wings from rocks kicked up by the landing gear. - There is an inherent slight pitch up when accelerating as the tail has a negative incidence and gets "blown" due to being directly behind the propellers (spinning in opposite directions, down toward the centre). -…
Hi reesen have a good look at Jon’s videos on drawing on his videos about drawing up models on fusion 360 and see his way of doing it. If you want to see the diagonal ribs Look up internal wing structures for 3D printing on you tube there is a lot of information there. There is videos on how to create the ribs I can draw RC p,Ames on Fusion 360 and I have created diagonal ribs but it takes a lot of learning but is interesting to see how it is done. depending on how far you want to go with drawing and printing. I have printed both types of wing structures and personally feel the best method…
Where can I learn more about the wing design for 3D printing? I noticed a lot of 3D printed wings have a curved rib like structure. I've also seen a wing with something similar to three spars. I would like to create a control line model in Fusion 360 and perhaps compare several internal wing structures. I bought an Ender 5 Pro and it's been an exciting learning experience.
I agree with your statement here, I have tried 2 different 3D RC companies plans and there print instructions. Both are very different but I found that a blend of the 2 make for great printing. On both I have found that there could be slight improvements. On both I have found that they could haves small improvement on some items. I have even redrawn them to my spec. And printed them. This is a hobby and is a new way to build our planes I am loving printing in 3D due to the flexibility it offers. If there are items that some are not happy with, improve on it and let the designer know of your improvements, don’t comp…